API Pipes
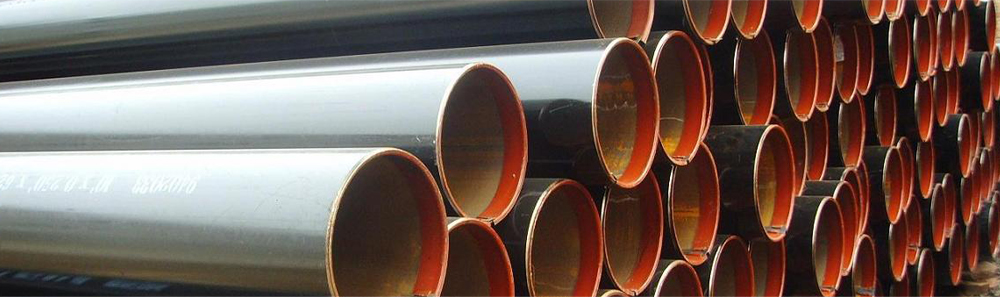
Electric welded pipes in the HFW (High Frequency Welded) category are rapidly gaining recognition for high integrity applications within the Oil & Gas sector. Their acceptance stems from several key advantages:
- Enhanced Dimensional Control: HFW pipes boast improved dimensional accuracy throughout their length, facilitating efficient coating and field joint integrity, crucial in demanding applications.
- Precise Mechanical Properties & Surface Quality: Leveraging the inherent qualities of hot-rolled coils, HFW pipes ensure precise control over mechanical properties and surface finish, ensuring consistent performance and reliability.
- Minimal Material Input for Welding: With no extraneous material introduced during welding, HFW pipes benefit from reduced impurities and vulnerabilities, further fortified by the utilization of state-of-the-art forming and solid-state HF welding technology.
The High-Pressure Line Pipe Manufacturing facility, situated at our Jangalpur Works in Howrah, West Bengal, is dedicated to producing HFW pipes to exacting standards. Capable of manufacturing pipes with diameters up to 20" and thicknesses up to 14.3 mm, our facility caters primarily to the needs of long-distance transmission of high-pressure oil, gas, and mineral slurry, as well as serving the drilling industries and other applications requiring high test pressure capabilities.
API & Line Pipe | |
Production Capacity | 150000 MT per annum |
Manufacturing Process | Solid State HF Welding with Seam Normalizing |
Outside Diameter | |
Thickness Range | Up to 0.562"(14.3 mm) |
Pipe Length | SRL/DRL/TRL (6 meters to 18 meters) |
Specifications | API5L/API 5CT/ASTM/UL/EN/ISO/IS/CSA Z245.1 & Client Specifications |
Pipe Ends | Beveled or Plain End |
Protective Coating | Bare or Rust Preventive Coating & Special coating for Line pipes. |
End Protection | Protected with Plastic /Metallic Caps |
Coating Application in Main Line Pipes
Current coating use on high pressure pipelines is dominated by FBE and 3LPE,3LPP finding increasing use for high temperature applications above the acceptable temperature range for mono-layer.FBE and PE with ISO specifications developed for these coatings.Excellent specifications have been developed by the CSA, and others for both FBE and 3LPE.
3 Layer PE/PP/DFBE/ & Internal Liquid Epoxy Coating Facility | |
Production Rate | |
Outside Diameter | Up to 20" (508.0 mm) |
Pipe Length | Up to 18 Meters |
Coating Specifications | |
End Protection | Protected with Plastic/Metallic caps |